Cement Optimized Spoke To Tom Tietz Of The California Nevada Cement Association About Efforts To Meet The Golden State’s Ambitious Carbon Reduction Goals.
By Jonathan Rowland
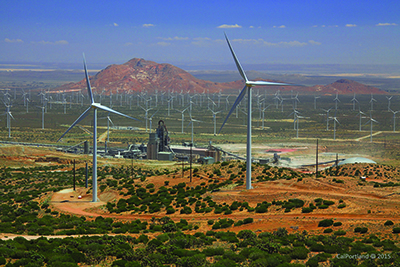
Among U.S. states, California is known for its progressive approach to carbon reduction. For example, for more than a decade, it has been the only U.S. market that requires cement producers to comply with a cap-and-trade program. The future is also “dynamic,” said Tom Tietz, executive director of the California Nevada Cement Association (CNCA), “given California’s ambitious pace to decarbonize.”
Under state law, the greenhouse gas (GHG) intensity of cement consumed in California must fall by 40% by 2035 compared to a 2019 baseline and reach net zero by 2045. “This creates unprecedented challenges and opportunities for the seven companies that produce and import cement into the Californian market,” continued Tietz.
According to the U.S. Geological Survey (USGS), the state produced about 9 million tons of portland and blended cement in 2023, down from almost 9.7 million tons in 2022. The Californian market comprises seven plants:
- CalPortland Mojave, Oro Grande, and Redding.
- Cemex Victorville.
- Mitsubishi Cement Lucerne Valley.
- National Cement Lebec.
- UNACEM Tehachapi.
Several of these companies also operate cement terminals throughout the state:
- CalPortland: National City, Stockton West and East, Santa Fe Springs, Union City, and Wilmington.
- Cemex: El Centro, La Mirada, Long Beach, Sacramento, San Diego, Richmond, Redwood City, and West Sacramento.
- Mitsubishi Cement Long Beach.
Eagle Material’s Nevada Cement, whose Fernley plant lies just over the state line, also operates cement terminals in Redwood City, Sacramento, and Stockton. Pan Pacific Cement, which also runs a terminal in Sacramento, completes the picture.
“Each Californian cement producer has a built-in incentive to improve GHG emissions intensity because the allowance allocation rate in the state’s cap-and-trade system is tightening over time,” Tietz explained. “Additional decarbonization requirements build a compelling need for each company to make plans that are unique to each plant and location.”
In 2021, the companies collaborated with CNCA to create a clear, actionable roadmap for achieving carbon neutrality. The updated roadmap from 2023 identifies three pathways and eight levers to achieve this goal, including short-term levers such as blended cement, alternative fuels, and heat recovery, as well as longer-term levers like renewable natural gas and carbon capture use and storage, which is the “biggest and most difficult lever of all,” noted Tietz.
Community and Government Engagement
On the federal level, Californian producers have received various grants to promote sustainability-related initiatives. According to Tietz, the “most notable” is the 2024 U.S. Department of Energy’s (DOE) Office of Clean Energy Demonstrations (OCED) award of up to $500 million to National Cement to decarbonize its Lebec cement plant.
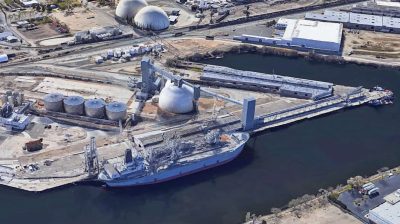
The plant has operated since the 1960s, supplying the southern Californian market. The grant application included a suite of emission-reduction technologies, including fossil fuel-fuel substitution using locally sourced biomass from agricultural byproducts, the production of calcined clay as a lower-carbon clinker alternative, and carbon capture of the plant’s remaining 950,000 metric tonnes of annual CO2 emissions.
Another California company, Oakland-based Brimstone, was also awarded OCED funds to construct a first commercial-scale plant using the company’s deeply decarbonized cement production process. According to the company, its process uses calcium silicate rocks to manufacture ordinary portland cement and supplementary cementitious material while passively removing atmospheric CO2.
At the state level, “a crucial part of collaborating with agencies is first emphasizing that a vibrant local cement industry is vital to the state economy and for addressing climate challenges,” continued Tietz. “While individual companies interact with their local jurisdictions on plant-specific topics, the California cement industry has developed a highly respected reputation for collaborating with state regulators and legislators. Our cement producers share a common message that they cannot achieve carbon neutrality on their own but invite all interested stakeholders, including state and local governments, to join in constructive dialogue about how to reach net carbon neutrality no later than 2045.”
Tietz also noted demand-side support for greener cement in the state, which is helping efforts to decarbonize cement production. “Private investors from the state’s world-leading tech industry might be the most high-profile of these supports, but many others are involved,” the association’s executive director said. “State and local agencies have enacted codes that limit embodied carbon in concrete and other materials, while environmental advocacy groups have promoted legislation aimed at advanced funding commitments for emerging materials and are promoting demand-side policies. Here at the CNCA, we regularly interact with architects, engineers, and contractors to provide education and help remove barriers to specifying blended cement.”
However, this is an ongoing process. “Attention continues to be given to the stakeholders throughout the value chain, where lower carbon options can still be blocked for use on construction projects,” he said.
Challengers Facing Carbon Neutrality
According to Tietz, two primary challenges to achieving net-zero cement stand out. The first is leakage. “Under current policy, California cement producers do not compete on a level playing field with imported cement that is not subject to the same regulatory costs as cement produced within the state,” he explained. “This makes it difficult to pass through the costs of decarbonization projects and affects producers’ confidence to invest in capital-intensive, transformational technologies to reduce GHG emissions.”
The second challenge is permitting. “While California has aggressive climate goals, a complex permitting system, extended timelines, and related litigation can dramatically increase the uncertainty associated with construction timelines and payback periods. There is a clear need to streamline and de-risk the permitting process.”
Despite some “bright spots” with alternative fuels, permitting has also slowed the adoption of circularity in the California cement sector. So-called departing load charges levied on cement plants generating some of their electricity using carbon-neutral technologies also made investments in self-generation financially unappealing.
“California is one of the few states applying such charges, which is why we were happy to see the passage of CNCA-sponsored legislation, Assembly Bill 2109: Industrial Process Heat Recovery, which aims to phase them out,” said Tietz.
The Future and Role of the CNCA
Decarbonizing cement and concrete is a “team effort,” said Tietz. “We are collaborating and contacting all interested stakeholders to join us in constructive dialogue about reaching net zero by 2045. This means facilitating productive engagement between the industry, policymakers, regulators, academics, environmental advocacy groups, and other interested stakeholders about how to accelerate progress, maximize the odds of success, and position California as a frontrunner in the global race to help ‘difficult-to-decarbonize’ industries reach net zero.”
Tietz concluded, “A foundational concept of creating undeniably resilient materials with cement, combined with reducing embodied carbon impacts, leads to concrete being the ‘no compromise’ material of choice. Creating the clearest and most direct path towards that future is an aspirational and essential foundation for long-term success.”